3 Things You Should Know About Beach Balls


In summer beach activities, one of the most indispensable is to play beach ball.Inflatable beach balls are often used for water play and beach games.Unlike common basketballs, footballs and volleyballs, it is thinner and larger in size. This makes it lighter and more easy to propel it.
The size of beach balls can be from 15cm to 150cm, and larger sizes can also be achieved in some special needs.Ordinary beach balls usually have 6 oval soft plastic panels, with two circular end panels, one of the end has a valve.When in use, you only need to use your mouth or an air pump to inflate it.
Below, I will introduce the production process of beach balls.
How are beach balls produced?
Before production, firstly, we have to decide the color and thickness of the ball.Usually, the thickness of the beach ball can be from 0.15mm to 0.18mm.After confirming this information, we can order PVC materials from PVC production factory. The material production cycle is generally about 15-20 days.Once the material arrives at our factory, we can start the first step: cutting
The material that has just been produced is in rolls.Many products usually require printing before cutting. But a classic beach ball doesn’t need to be printed. It can be made using panels that are already colored.In the factory, there are usually two main ways to cut materials.One is to use a machine to cut a printed roll of material into pieces one by one.The other is by hand, cutting the solid-colored material into smaller pieces. As we mentioned earlier, the beach ball consists of 6 oval soft plastic panels, with two circular end panels. These panels are cut directly from the materials. The roughed material is stacked together into the die cutting machine.Workers place sharp molds on top of the material, push them into the machine, and start the machine. Under the enormous pressure of the machine, the sheet of material is cut into the shape of the mold. Workers will take out the mold and take out the panels inside. These panels would be stacked together and sent for next processing.
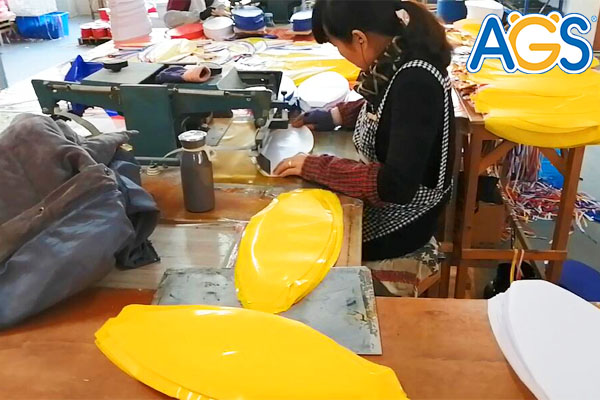

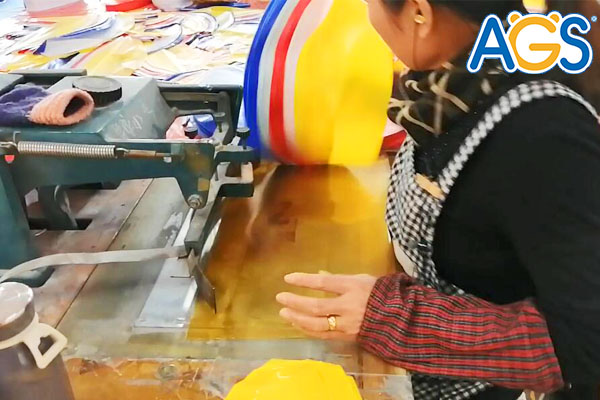
Then we came to the most important step in making inflatable PVC products – high frequency stamping. In there, workers use a machine called a “high frequency” to stitch the individual panels of the product together. In the production process of ordinary beach balls, workers will put a piece of yellow panel at the bottom, and then take a piece of white and put it on top of the yellow one. Next, workers place the two pieces of material into a high-frequency machine with a curved die. Driving this machine, the mold transmits high temperature and pressure to press the two panels tightly together.After completing this step, fold the top piece of white material outwards.Meanwhile, take another red panel and place it on top of the folded white panel.Repeat the process of putting into the machine.Until 6 pieces of material are spliced together in the order of yellow, white, red, white, blue, and white, the first high-frequency process is completed.
These simply spliced panels would be sent to the next place.In there, workers would use molds that were curved at the ends and hollow in the middle.They used this special mould to stamp out two short lines on the yellow panel at the front and the white panel at the back.This is to make subsequent processing more convenient.

Then you need to splicing the upper and lower round panels to the half-finished product.The two round panels are different. One of them has a hole in the middle, where a PVC air valve is installed.The other is complete, usually with the product’s warnings and tracking labels printed on it.Workers place the parts to be spliced on top of the cylindrical mold.Then place the round panel on top. A ring-shaped embossed die is installed on the high-frequency machine. When the machine is turned on, the die will press the panel tightly against the other PVC parts.By splicing two circular panels to the other, the production of the beach ball is more than half completed.
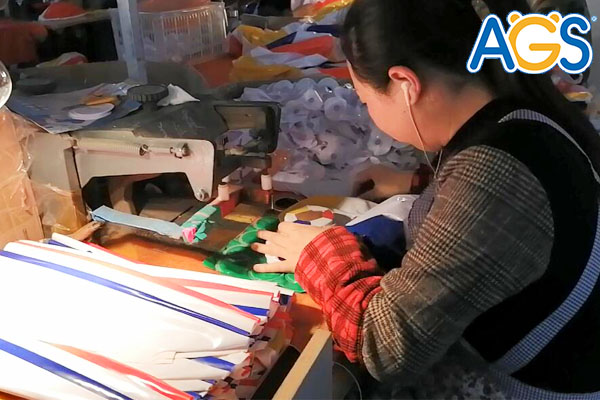

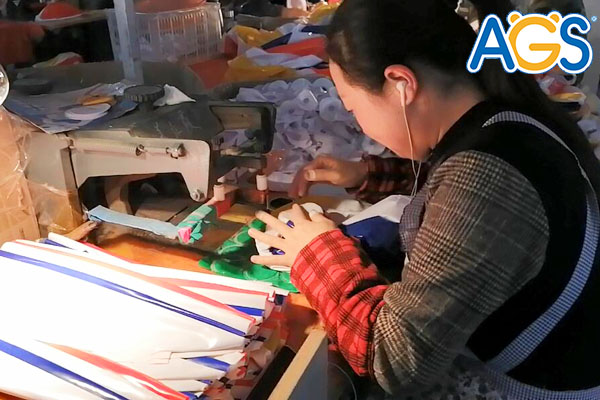

Finally, the semi-finished beach ball will be transferred to the last high frequency machine. Workers use a high-frequency machine with a curved die to connect the openings of the beach balls together.Tear off the excess edge of the beach ball, and the whole beach ball is finished.


However, this is far from enough. There are still many steps to be done before beach balls can be placed on supermarket shelves.
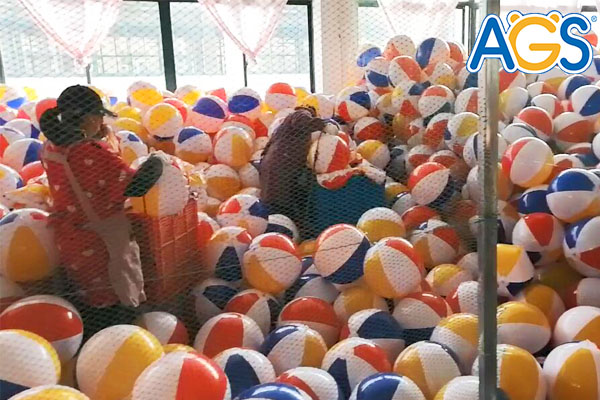
All beach balls, and even any of our other PVC inflatables, require an inflation test at the factory.Although it may be hard to imagine,but this is actually a very huge project. The relevant person needs to fully inflate each product.The quantity of our finished products is very large, usually several thousand, sometimes even tens of thousands.So these inflated products are often stacked as high as mountains, often covering all the room.Once full of air, they will be left here for more than 24 hours.When there is no air leakage after 24 hours, our products are considered to have passed the preliminary quality inspection.


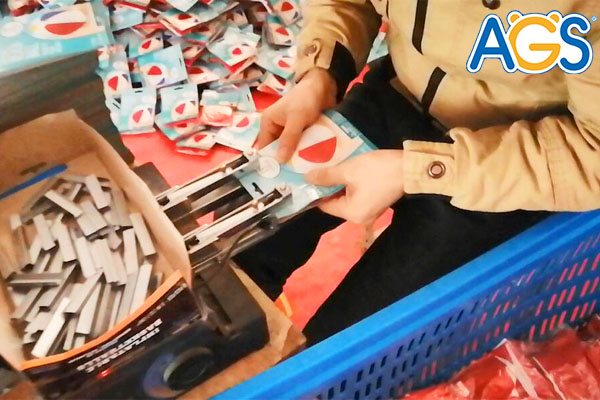
After inflation test, the valve of these beach balls is opened and a small hollow hose is inserted.This hose will allow excess air inside to leak out. Then the worker can start the packing.The workers first take out the hose from the gas nozzle, and then use their hands to smooth the surface of the wrinkled beach ball.Next, workers will fold the beach balls to the appropriate size and put them in the packaging plastic bags.Finally, the worker staples the color card which printed the product information to the opening of the plastic bag.
The production of beach balls is now complete.These beach balls are then packed in shipping cartons and shipped around the world.
How to order beach balls?
If you are selling these products, if you want to order some freebies with your own logo, then AGS Industry Group are definitely your trusted manufacturer.We have very professional experience in mass customization.Over the past twelve years, we have produced a large number of products for customers all over the world.
Here’s some information you might want to know.
Minimum order quantity(MOQ)
3600pcs or more.Our MOQ is based on the order quantity of raw materials.We need to order materials from a factory that manufactures PVC materials.Raw materials cannot be purchased if the quantity is too small.
Sample
For the product you want to customize, we can make a sample for your reference.But we do not provide free samples. The cost to make a sample is usually $100-200. This price includes making molds, printing and paying labor costs.We don’t make money from samples, and even pay extra to produce samples.
Delivery time
The daily production capacity of our workers is about 30,000PC, but due to the large number of orders from customers, our production time is different as follows: regular quantity, about 30 days after sample confirmation; Large quantity, according to the quantity.
Price
The price of a beach ball usually between $0.2 to $5.Price is affected by craftsmanship and quantity. Generally speaking, the more quantity ordered and the simpler the craft used, the cheaper the beach ball will be. Moreover, our prices are also affected by the prices of raw materials.
What are the testing requirements for beach balls?
If you’re interested in ordering some beach balls, the next thing you may think about is whether the materials they use are safe and environmentally friendly, or what tests do they pass.
Here, we will briefly introduce you to some test-related knowledge.
Our materials are all 10P and above.P stands for Phthalate. The higher the number in front, the healthier it is for the human body.
For Europe, the most common test is EN71-1/2/3.This is the test that most toy products need to pass.Products that pass this test can get CE certification.
EN 71-1: Mechanical and physical properties
It checks whether any mechanical or physical features of the toy could harm the child while playing/using.
It also includes determining if there are sharp points on the toy, or if the toy has parts that can be easily swallowed.
EN 71-2: Flammability
It will confirm whether the toy can cause injury to children due to its flammability. These include determining whether any prohibited flammable materials are present in children’s toys, how long the item burns and how quickly the flames spread over it. Different types of items have different pass rates.
EN 71-3: Specification for migration of certain elements
This includes the detection of the content of some specific elements in the product.This is to confirm whether the product is safe enough for the human body.
For the US market, testing for Prop65 is usually required.Lead content, ASTM, CPSIA, are also common tests.For the North American market, their tests are all similar.
Of course, most importantly, you can seek more professional advice from your local laboratory.Never forget this.



We all know, beach balls are used as a toy.In addition to the most classic beach ball styles, we also have many other beach balls with different shapes.For the sake of beauty, many beach balls use transparent materials.It will be filled with some sequins, confetti, feathers, etc.There are some cute clear beach balls that will have another toy inside, which we call ball in ball.Likewise, there are many people who print advertisements on beach balls.A cheap and fun beach ball is a great advertising vehicle.Overall, beach balls are the signature product of summer fun. No one can refuse to play beach balls while enjoying the sun, beach and pool. They are both a party decoration and the most indispensable party toy.
The above is the introduction of beach balls. After that, we will continue to bring you the introduction of other interesting inflatable products. Looking forward to meeting you next time.